El aumento de los datos disponibles, la conectividad, la analítica, la interacción hombre-máquina y las mejoras en la robótica caracterizan la cuarta revolución industrial. La ola de cambios digitales que comenzó a mediados de la década de 2010 no muestra signos de desaceleración, y los fabricantes deben adoptar todo lo que la Industria 4.0 tiene para ofrecer para seguir siendo competitivos.
La tecnología de la información (TI) está impactando los procesos de manera fundamental a medida que las líneas entre la TI y la tecnología operativa (OT) se vuelven borrosas. La OT está representada por el hardware de la fábrica: los dispositivos que realizan el trabajo real. En muchos casos, estos equipos ya están automatizados, pero a menudo de forma fragmentada e insular, de modo que sólo unas pocas máquinas que afectan a una determinada parte del proceso están integradas y comunicadas. Con la Industria 4.0, toda la maquinaria, los sistemas de control y los sistemas de TI estarán conectados horizontal y verticalmente en toda la organización, cooperando para optimizar los procesos y la productividad.
Las plantas de producción conectadas permiten a las empresas monitorizar los equipos y la maquinaria, haciendo un seguimiento de los estados en cualquier momento. Aprovechar los datos disponibles de sus máquinas significa que los fabricantes pueden mejorar el rendimiento, ayudar a prevenir fallos en los activos y tomar decisiones basadas en hechos que, de otro modo, podrían dejarse a las conjeturas.
Abrazar la revolución
Si bien las barreras percibidas para la implementación completa de la Industria 4.0 incluyen el costo, el conocimiento de los empleados y el tiempo, Videojet está ayudando a los fabricantes a aprovechar la conectividad de sus sistemas de impresión, etiquetado y marcado láser con una ideología de “nacido digital”. Estas impresoras Videojet producen dos conjuntos de datos: datos operativos que se relacionan con los requisitos propios de la impresora y datos de proceso que describen lo que está sucediendo en la línea de producción.
El Wi-Fi permite que las impresoras y láseres digitales Videojet nazcan con una fácil conectividad a las redes internas de un fabricante sin necesidad de cables ni cableado. Las conexiones celulares integradas, cuando estén disponibles, se comunican entre la nube de Videojet y la impresora y eliminan la necesidad de utilizar la propia infraestructura de TI del fabricante. Las impresoras Videojet habilitadas para móviles están equipadas con tarjetas e-SIM para garantizar que la impresora seleccione el operador con la mejor señal telefónica disponible en una región.
En una planta de fabricación, un cliente de Videojet adoptó sin reservas la filosofía de “nacido digital” y conectó en red su flota de impresoras Videojet, lo que dio como resultado la eliminación de los errores de codificación de fechas en la planta. Dado que todos los datos de codificación del producto ahora se controlan de forma centralizada, los operadores pueden simplemente escanear una orden de trabajo y el sistema envía la fecha correspondiente a cada impresora. El sitio ahora se utiliza como ejemplo de “Best Practices” para los nuevos proveedores de la empresa.
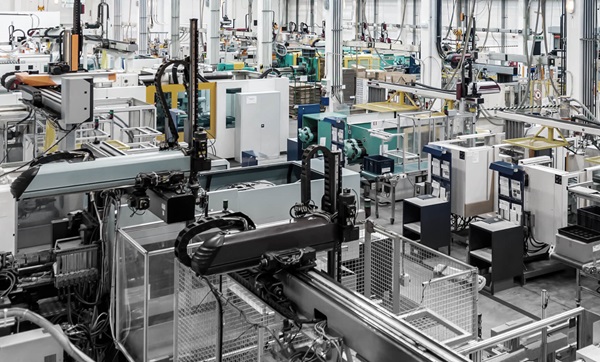
Datos a nivel de impresora
Con las últimas soluciones de Videojet, los responsables de las fábricas pueden realizar un seguimiento de las velocidades de producción, las tasas de error y el rendimiento de los equipos con una precisión sin precedentes. Por ejemplo, la avanzada impresora de inyección de tinta continua (CIJ) Videojet 1880 + cuenta con 53 sensores que supervisan los procesos en tiempo real. Los sensores realizan un seguimiento del rendimiento de la impresora y siguen la secuencia de eventos para detectar posibles fallos.
Con varios componentes supervisados, la resolución de problemas es rápida y precisa con el Videojet 1880 +. Por ejemplo, si la velocidad de la bomba ha disminuido y registra una temperatura de funcionamiento más alta de lo habitual, la causa puede ser una obstrucción en el flujo de entrada de aire de refrigeración. Al leer los datos de varios sensores, la máquina puede autodiagnosticarse y sugerir los pasos necesarios para solucionar el problema. El objetivo es reducir las principales causas del tiempo de inactividad no planificado de la impresora.
Por supuesto, el tiempo de actividad es fundamental para la rentabilidad de cualquier negocio. Si bien las reparaciones de emergencia son costosas, el mayor daño al resultado final puede ser causado por el momento inesperado en que un activo está inactivo y no contribuye a la producción. Las paradas prolongadas pueden tener un impacto a largo plazo en las relaciones con los clientes si provocan retrasos o pedidos no cumplidos. Al aprovechar las funciones de mantenimiento preventivo de una impresora, se pueden reducir o evitar las reparaciones de emergencia.
Manténgase a la vanguardia con actualizaciones en tiempo real sobre las últimas noticias:
Datos a nivel de línea y de sitio
Al emplear impresoras y láseres como proxies, los usuarios pueden acceder a datos e informes que van más allá de los datos operativos, los diagnósticos y los controles de la máquina de una impresora o láser. Es posible la visibilidad de los datos de producción en varias líneas, así como el rendimiento de las líneas individuales para determinados días, turnos y tiradas de producción. Las proyecciones para las tasas de ejecución actuales y mejores ayudan a determinar si una producción está en el objetivo, mientras que la OEE se puede rastrear por hora a lo largo de un turno. Los usuarios pueden extraer datos clave directamente en sus propios sistemas, lo que facilita la creación de paneles de control y la integración en los sistemas de mantenimiento existentes.
Impulsando mejoras futuras
Con el permiso de los clientes, Videojet está recopilando datos analíticos anónimos de toda su población de impresoras para sacar conclusiones de las diferentes condiciones de funcionamiento. Esta información se utiliza para mejorar la fiabilidad del hardware de la impresora y proporcionar datos de rendimiento que pueden ayudar a evitar el tiempo de inactividad no planificado con el uso de análisis e inteligencia artificial (IA).
La conectividad en las máquinas de codificación y marcado no se limita a mejorar la recopilación de datos y la toma de decisiones, sino que es un catalizador de un cambio fundamental en la forma en que los fabricantes interactúan con sus procesos de producción. A medida que evoluciona el panorama de la fabricación, el futuro promete no solo líneas de producción más rápidas, sino también procesos de fabricación más inteligentes y sostenibles.